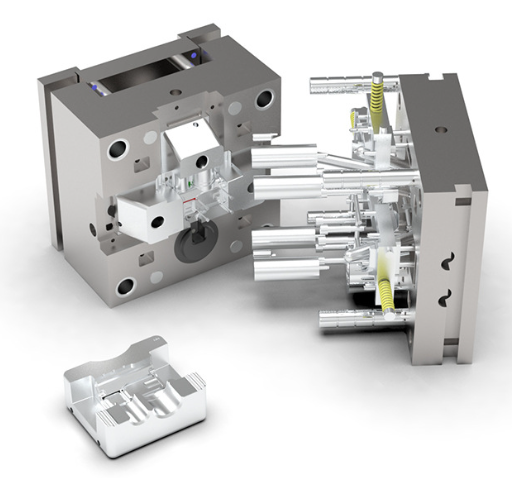
- Aperçu
- Demande d'information
- Produits connexes
Un moule de fonderie sous pression est un outil utilisé pour fabriquer des pièces en métal par le procédé de fonderie sous pression. Il est généralement fabriqué en acier allié de haute résistance ou d'autres matériaux résistants à l'usure, avec une structure complexe et des canaux internes précis pour répondre aux exigences de forme et de taille du casting. La fonction principale d'un moule de fonderie sous pression est d'injecter rapidement du métal fondu (comme l'aluminium, le zinc, le magnésium, etc.) dans la cavité du moule, de le refroidir et de le solidifier, puis d'obtenir les pièces métalliques souhaitées.
Les principaux composants du moule de fonderie sous pression :
1. Corps du moule
2. Cavité du moule
3. Système d'alimentation
4. Système d'évacuation
5. Système de refroidissement
Types de moules de fonderie sous pression :
1. Moule chaud : adapté aux métaux à faible point de fusion, comme les alliages de zinc, avec une vitesse d'injection rapide et une efficacité de production élevée.
2. Moule à essai froid : adapté aux métaux à haut point de fusion, comme les alliages d'aluminium, le métal fondu doit être placé dans une chambre froide avant l'injection.
Avantages des moules de fonderie sous pression :
1. Haute précision : peut produire des pièces moulées avec des dimensions précises et des surfaces lisses.
2. Formes complexes : peut produire des pièces métalliques avec des structures complexes.
3. Haut rendement de production : adapté à la production en série, économisant les coûts de matières premières.
4. Bonnes propriétés mécaniques : les pièces moulées ont une structure dense et une grande résistance.