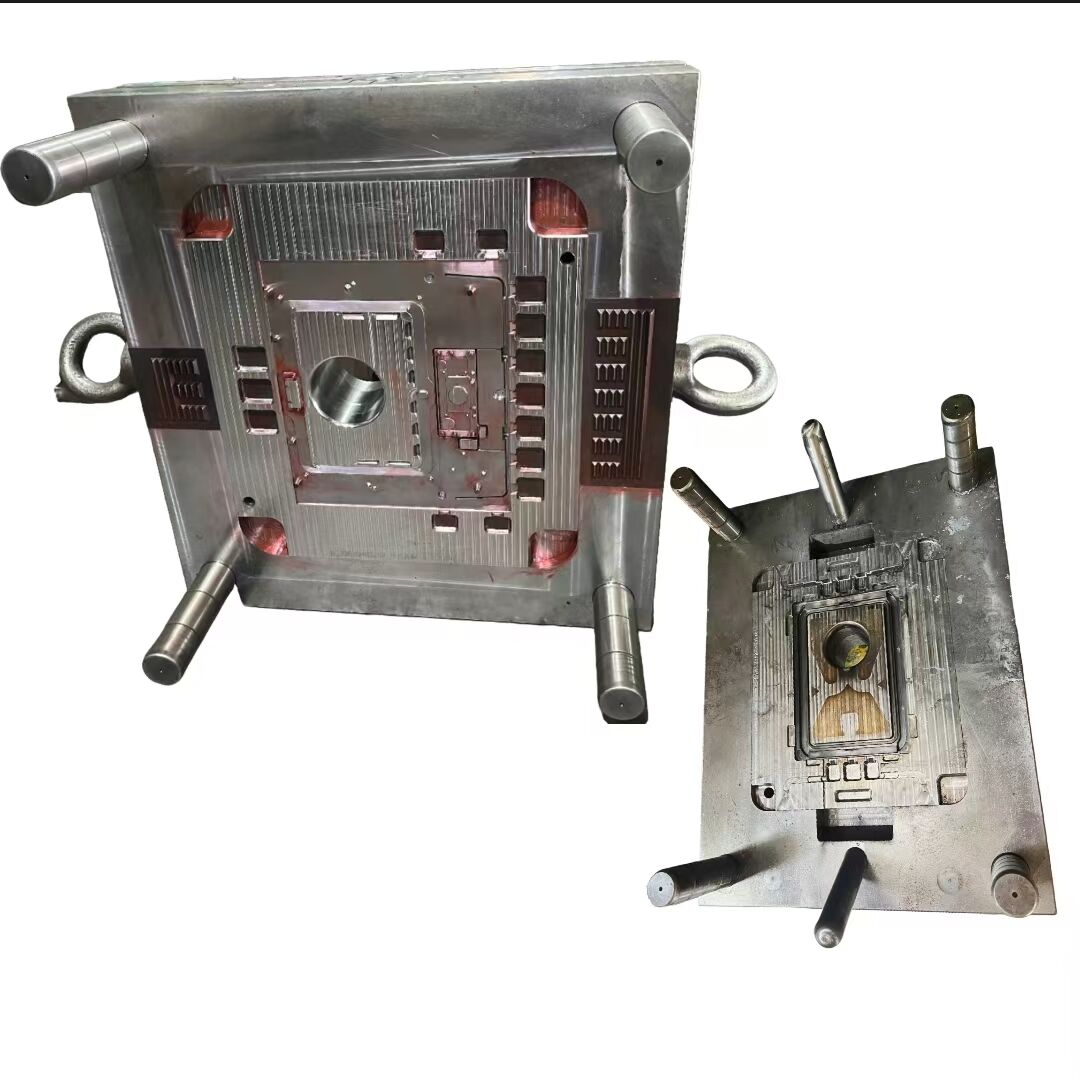
- Overview
- Inquiry
- Related Products
Our die casting molds, combining cutting-edge technology and innovative design, open the door to efficient production. Precise cavity structure ensures perfect molding of liquid metal with near-zero error. Intelligent temperature control system, so that each die casting in the ideal state of production, greatly improving production efficiency and product quality. Compared with the traditional mold, the die-casting cycle is greatly shortened, which helps you to seize the market opportunity. Each set of mold is our master craftsmen's heart and soul to complete, selected high-quality mold steel, after a number of fine processing procedures, to create a tough and durable mold body, unique runner design as smooth as blood vessels, so that the metal liquid evenly and smoothly filled, molded products have a smooth surface, the result is dense. Attention to detail, the pursuit of the ultimate, from the mold assembly precision to the surface treatment process, are our dedication to quality, to provide you with die-casting molds in the boutique.
From design to finished product, die casting production is a rigorous and complex process that involves a number of key steps, each of which needs to be precisely controlled in order to ensure the high quality and performance of the final product.
Product mold design: according to customer requirements and product specifications for product 3D modeling and mold structure design, design is completed using high-precision processing equipment to manufacture molds.
Raw material preparation and melting: according to the product characteristics of the selection of suitable die-casting alloy materials, such as aluminum alloy, zinc alloy and so on. Raw materials are put into the melting furnace and heated to liquid state, and the temperature is strictly controlled. Time and alloy composition ratio.
Die-casting molding: through the die-casting equipment will be prepared metal liquid into the die-casting machine mold cavity, die-casting machine through high-pressure fast metal pressure into the mold, so that it in the cavity quickly cooled and solidified molding. Here you need to accurately set the die-casting parameters, to ensure product molding quality and production efficiency.
After treatment and finishing: die-casting molding products need to carry out a series of post-treatment processes, including the removal of sprues, flying edge, surface treatment (such as shot blasting, sand blasting, electroplating, painting, etc.) to improve the appearance and improve corrosion resistance. For some parts of the requirements of high-precision products need to be CNC machining.
Quality inspection and control: Throughout the production process, comprehensive quality inspection and control is implemented, utilizing a variety of inspection means, such as CMM, spectral analyzers, etc.