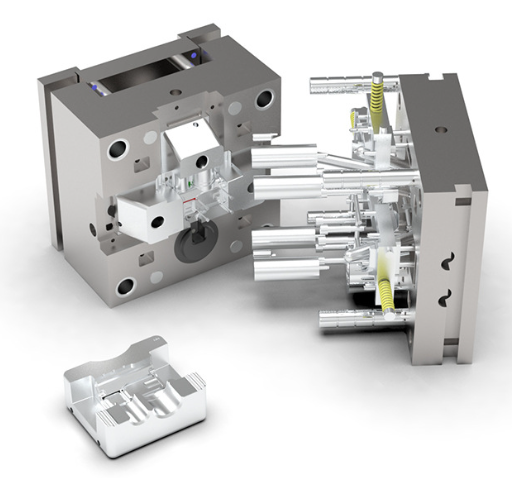
- Overview
- Inquiry
- Related Products
A die casting mold is a tool used to manufacture metal castings in the die casting process. It is usually made of high-strength alloy steel or other wear-resistant materials, with a complex structure and precise internal channels to meet the shape and size requirements of the casting. The main function of a die casting mold is to quickly inject molten metal (such as aluminum, zinc, magnesium, etc.) into the mold cavity, cool it down and solidify it, and then obtain the desired metal parts.
The main components of the die casting mold:
1. Mold body
2. Mold cavity
3. Feeding system
4. Exhaust system
5. Cooling system
Types of die casting molds:
1. Hot mold: suitable for low melting point metals, such as zinc alloys, with fast injection speed and high production efficiency.
2. Cold test mold: suitable for high melting point metals, such as aluminum alloys, the melting point metal needs to be placed in a cold chamber before injection.
Advantages of die casting molds:
1. High precision: can produce castings with precise dimensions and smooth surfaces.
2. Complex shapes: can produce metal parts with complex structures.
3. High production efficiency: suitable for mass production, saving raw material costs.
4. Good mechanical properties: the castings have dense structure and high strength.