Exploring Aluminum Die Casting: Techniques and Applications
What is Aluminum Die Casting?
Aluminum die casting is a manufacturing process where molten aluminum is injected into molds to produce complex shapes and components with high precision. This technique involves using high-pressure systems to ensure that every detail of the mold is captured, leading to superior surface finishes. The method is valuable because it combines precision with speed, enabling rapid production cycles that are crucial in various industrial applications.
The aluminum die casting process ensures that products exhibit excellent dimensional accuracy and smooth surfaces, reducing the need for secondary machining. The high pressure used during the casting ensures that the finished products have intricate detailing and structural integrity. This precision is crucial for industries that require components with specific measurements and aesthetic qualities. Moreover, the process supports high-volume production at a lower cost, making it economically advantageous for manufacturers aiming to produce large quantities without compromising quality.
Key benefits of aluminum die casting include its ability to produce lightweight yet durable parts essential in fields like automotive, aerospace, and consumer electronics. The die casting products maintain a good stiffness and strength-to-weight ratio, are resistant to corrosion, and offer excellent electrical conductivity. This is why many manufacturers opt for aluminum die casting when looking to balance performance with cost-effectiveness in their production lines. As a result, aluminum die casting manufacturers can deliver products that meet the demand for complex and reliable components in numerous industrial sectors.
Key Techniques in Aluminum Die Casting
Aluminum die casting is a versatile manufacturing process that incorporates several techniques, each with distinct advantages. High-pressure die casting is the most commonly used method, employing intense pressure to inject molten aluminum into a durable steel mold. This technique ensures rapid production rates and precise part dimensions, making it a popular choice for mass production.
Vacuum die casting improves product quality by minimizing defects such as porosity. By removing air from the die before injection, this technique facilitates the creation of components with enhanced structural integrity and aesthetic appeal. Consequently, it is suitable for applications requiring high reliability and minimal flaws.
Squeeze casting merges casting and forging processes. This method involves applying pressure to the molten aluminum within the mold, resulting in parts with superior strength and density. Industries that require high-performance, durable components often rely on squeeze casting for its remarkable material properties.
Semi-solid molding utilizes an alloy that is only partially solidified, optimizing flow conditions and enabling the production of intricate geometries. This process results in components with improved mechanical properties, such as increased strength and reduced porosity compared to conventional casting methods.
Gravity die casting is ideal for larger parts, as it relies solely on gravity to fill the mold. While this method offers slower production rates and greater variability than others, it remains a viable option for parts where precision is less critical. It is valued for its simplicity and lower tooling costs.
Lastly, low-pressure die casting involves using controlled low pressure to direct the molten aluminum into the mold, minimizing turbulence. This technique allows for finer wall sections and is instrumental in creating larger, complex structures with superior finishes. Each of these methods offers unique benefits, providing manufacturers with the flexibility to choose the best process for their specific application needs.
Applications of Aluminum Die Casting
Aluminum die casting is pivotal in the automotive industry, where its applications underspin advancements in vehicle design and efficiency. Components such as engine parts, transmission housings, and various structural elements benefit from the lightweight and robust nature of aluminum die casting. This application significantly contributes to the reduction in overall vehicle weight, thereby enhancing fuel efficiency and performance. The advanced [aluminum alloys for die casting](#) ensure that these automotive parts meet rigorous safety and durability standards.
In the electronics sector, the use of aluminum die casting is essential for manufacturing housing parts that require efficient thermal management. The thermal conductivity and heat dissipation properties of aluminum castings make them ideal for encasing electronic devices. Additionally, the corrosion resistance and adaptability of aluminum die casting allow for detailed, complex shapes, necessary for modern electronic equipment. Die cast aluminum housings protect sensitive components while dissipating heat effectively, ensuring improved product longevity and reliability.
The aerospace industry also takes advantage of aluminum die casting's attributes to fabricate components like brackets and structural frames. These parts demand high precision, reduced weight, and exceptional strength, characteristics that aluminum die casting readily provides. By using aluminum die casting, manufacturers can meet aerospace standards that are crucial for safety and performance. Furthermore, the ability of aluminum die casting to produce large and complex parts with consistent quality helps in maintaining production efficiency in aerospace manufacturing.
Industries that utilize heavy machinery, such as the industrial equipment sector, often incorporate aluminum die cast parts due to their durability and cost-effectiveness. Components for pumps, compressors, and valves are manufactured using aluminum die casting to enhance performance and lifespan while minimizing costs. Because aluminum parts are lightweight yet robust, their use can lower transportation and operational energy needs, providing substantial savings over the machinery's life cycle.
In the world of lighting, aluminum die casting enables the creation of innovative, aesthetic, and energy-efficient lighting solutions. Its flexibility allows designers to create intricate and dynamic shapes with excellent surface finishes. Beyond aesthetics, aluminum die castings deliver high performance in terms of durability and heat management, proving essential for both traditional and LED lighting technologies. The capacity to create both functional and decorative designs highlights the versatility of die-cast aluminum in solving modern lighting challenges.
Aluminum Alloys for Die Casting
Aluminum alloys play a crucial role in the die casting process, offering unique properties tailored to specific applications. Among the various alloys, the A380 Aluminum Alloy is renowned for its excellent fluidity and corrosion resistance. This makes it ideal for casting intricate shapes and producing detailed components, especially in environments where durability is paramount. Industries like automotive and consumer electronics often favor A380 for its balance of versatility and strength.
Turning to A356 Aluminum Alloy, its high strength-to-weight ratio is a standout feature. This alloy offers excellent mechanical properties, making it a prime choice for aerospace and automotive applications where both durability and lightweight characteristics are crucial. The alloy accommodates the structural demands of these industries, contributing to fuel efficiency and compliance with safety standards.
A383, also known as ADC12, is distinguished by its good castability and low shrinkage rates. These characteristics reduce defects during production, resulting in higher quality cast products. Manufacturers turn to A383 for applications that require reliable performance under manufacturing pressures, ensuring efficiency in various production lines.
A360 Aluminum Alloy is valued for its high corrosion resistance and electrical conductivity. These properties make it an excellent choice for electronic housings, where protection from both environmental and operational stresses is necessary. Its adaptability ensures that products maintain performance in diverse electronic device applications.
Lastly, A413 Aluminum Alloy is preferred in scenarios demanding high fluidity and dimensional stability. This is especially important for thin-walled sections, where precision and uniformity are crucial. The alloy's application in these niche areas showcases its utility in balancing fluidity with the structural integrity needed in high-stakes manufacturing environments.
The careful selection of aluminum alloys is paramount for die casting, with each alloy bringing specific advantages to the table. This tailored approach ensures that industries leverage the most suitable material, optimizing both performance and production efficiency in aluminum die casting products.
Exploring Aluminum Die Casting Products
Aluminum die casting products are crucial in various industries, thanks to their precision engineering and versatility. The aluminum die casting mold is a prime example, designed meticulously to ensure the optimal flow of molten aluminum. This process showcases the capabilities of die casting, making it indispensable in manufacturing precise components with enhanced quality. Molds are critical in shaping intricate designs, emphasizing the strength and adaptability of aluminum die casting products.
Precision die casting services leverage advanced technology to craft high-quality parts with tight tolerances. These services are tailored to meet clients' specific requirements, ensuring that every part produced adheres to exact specifications. The use of cutting-edge machinery and skilled craftsmanship allows for the manufacture of components that epitomize precision and excellence. This service is essential for producing parts that are not only durable but also consistently meet industry standards.
Aluminum die castings cover a vast array of products that illustrate the effectiveness of aluminum in diverse industries. These include automotive components, electronic housings, and construction materials. The adaptability of aluminum die casting to various applications underscores its importance and the broad range of products it can produce. This versatility is a testament to the process's capability to combine quality with quantity, satisfying commercial and industrial demands worldwide.
Custom parts in aluminum die casting are a focal point of design and innovation. The process involves a collaborative approach where client specifications dictate the design and function, ensuring parts that optimize performance and functionality. This customization potential highlights aluminum die casting's ability to meet diverse industry needs, from unique design specifications to the development of parts that enhance operational efficiency.
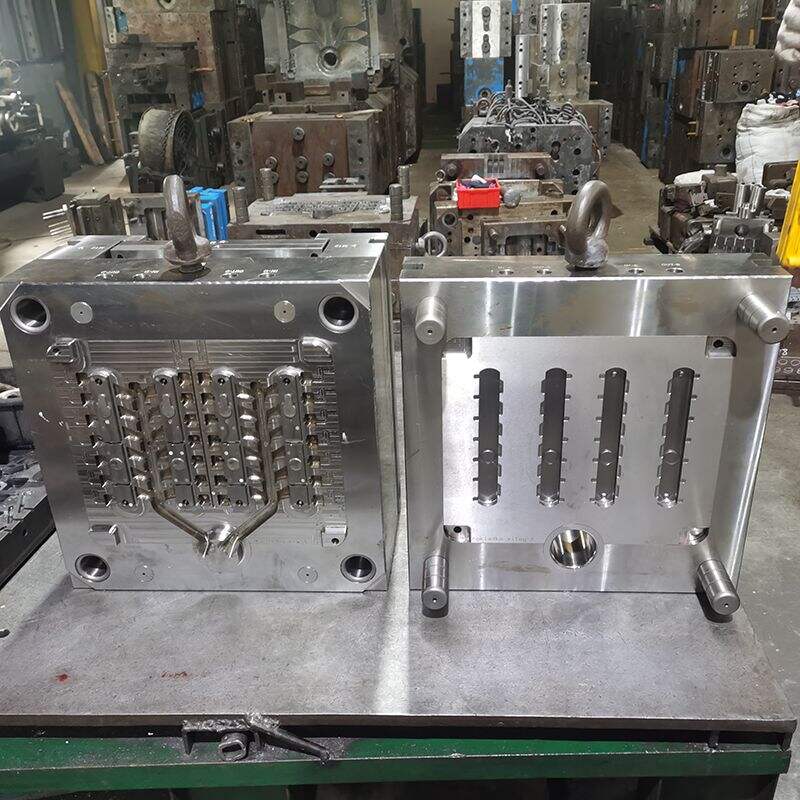
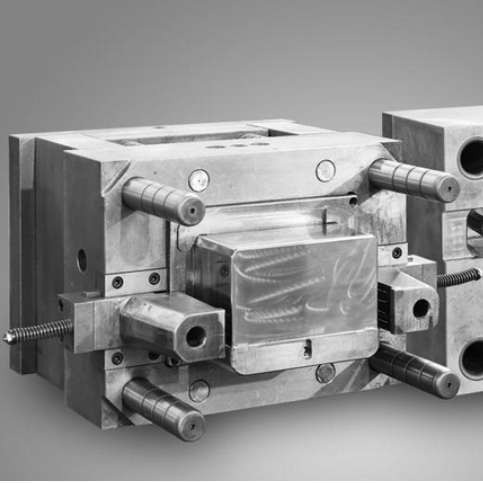
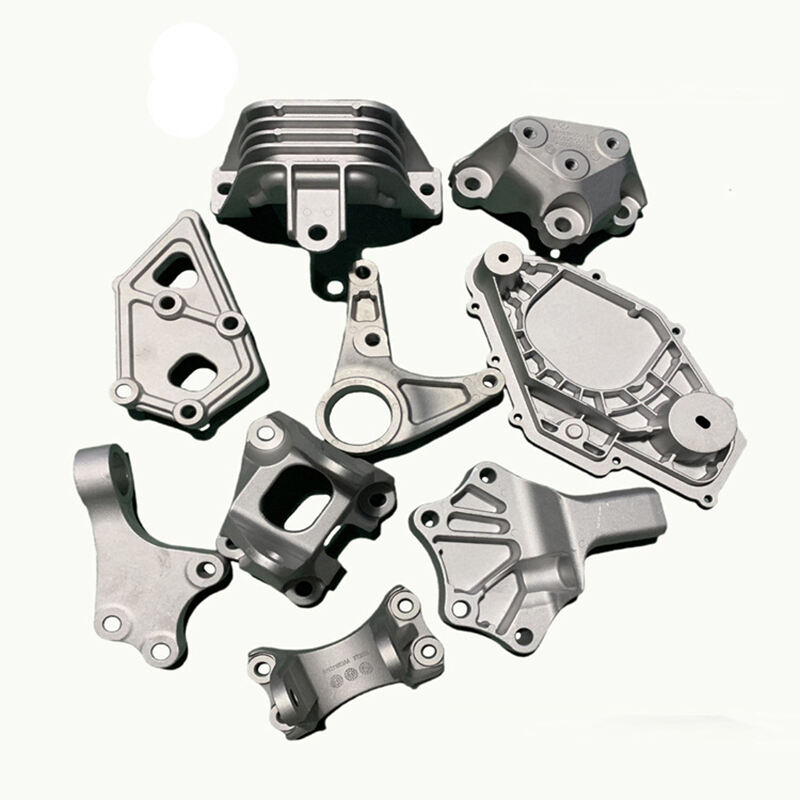
Environmental Impact and Sustainability
Recycling plays a pivotal role in minimizing the environmental impact of aluminum die casting. Aluminum is inherently recyclable, and its quality does not degrade after reuse. This characteristic allows aluminum die cast factories to melt down and repurpose scrap aluminum efficiently, significantly reducing industrial waste. By opting for recycling, industries not only lower their environmental footprint but also cut down raw material costs, promoting sustainability in die casting operations.
Moreover, the die casting industry is embracing energy-efficient technologies to curtail energy consumption and reduce the carbon footprint associated with production. Innovations such as automated pouring systems and advanced smelting solutions enable manufacturers to optimize energy use and enhance operational efficiency. These measures, together with the increased reliance on recycled aluminum feedstock, underscore the industry's commitment to sustainable practices and the responsible production of aluminum die casting products.